Written by Charles S. Pipes.
A good gas design goes electric as featured in the October 2013 issue of Model Aviation.
Download free plans of the PT-19.
As World War II approached, the US Army Air Corps (USAAC) believed that a low-wing, higher-performance basic trainer was needed. The government was looking for a more demanding basic trainer that would better prepare the fledgling aviators for the high-performance nature of the combat aircraft being developed. This led to the USAAC purchasing the Fairchild PT-19 two-seat monoplane in 1939, and to quote the movie Forrest Gump, “That’s all I have to say about that.”
I need to begin by thanking Robert Somers and giving him the lion’s share of the credit for the development of this model. I converted Bob’s good gas design into an excellent electric-powered aircraft. I cannot take credit for how well it flies. The fact that it has evolved into a great-flying airplane is because Bob’s initial work produced a light, stable gas model that took minimal effort to rework.
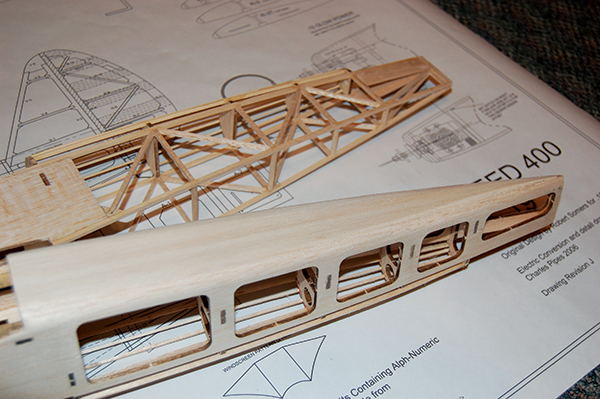
In transitioning from the original truss design to sheet construction, I rounded the corners of the fuselage to improve its appearance. His original design was a trussed structure built around an inverted O.S. Max .10 two-stroke with a 40-inch wingspan and weighing roughly 30 ounces dry. It had excellent flight characteristics with plenty of power for aerobatics. As I watched him fly it my only negative thought was that the .10, being inverted, tended to be slightly finicky to start. Shortly after seeing it fly, we decided to convert the design to a Speed 400-size electric. Bob graciously loaned me his original drawings. As a testament to Bob’s original design, the only structural change made was lengthening the nose. This helped achieve the correct CG with the lighter electric motors. I have an older version of AutoCAD, and decided to use it for the design. Having the CAD program on my laptop allows me to work on models while traveling and to select parts on the drawings and set them up for cutting. I chose to have John Valentine at Top Notch Product Company cut the parts. He is willing to work with builders going through the learning process of design layout. Because of the amount of travel required for my job, time in my shop is a premium and being able to email a cut file from a hotel and have the parts waiting when I get home is a great advantage. For the diehard scratch builder, I have made sure the plans show all of the parts so that the short kit is not mandatory.
Going Electric
Having flown only glow/gas models, I have considered electrics as toys. Similar to others of my generation, I carried the preconceived notion that an electric would be heavier and underpowered compared with any glow version. With this mentality I began working with the idea of cutting weight wherever possible, then learned that Bob is an advocate of light construction. As I made changes to switch to laser-cut parts and ease construction, I added weight to the basic airframe. As the model neared completion I purchased a set of digital scales and had trouble believing it weighed approximately 22 ounces with a 1,650 mAh LiPo. Bob and I have concluded that the weight savings was because of the availability of all the new “light” electric hardware. The electric motor, ESC, and battery weigh significantly less than the .10-size engine, fuel tank, tubing, and the throttle servo and its linkage. Other weight savings can be attributed to using the lighter microreceivers, servos, foam wheels, and lighter hardware. Using Solarfilm instead of MonoKote also reduced the weight.Features
The initial effort was a trace of Bob’s design where I laid out the parts in CAD and replaced the .10 O.S. Max engine with an E-flite 450 brushless outrunner. I carried the fuselage sides past the original firewall and drew the electric motor mounted to a laminated nose block ending in a plywood nose plate. The motor is accessed through a removable top hatch. The primary advantage to mounting the motor this way is that it eliminates the need for a separate fiberglass cowl. The most significant change at this point was to design the central fuselage into a tabbed and slotted-box design that made it easier to build the fuselage straight. Not wanting to have to turn the model on its back or take it apart to change the batteries, I designed a removable hatch for the cockpit area, providing access to the flight battery and servos. The motor and battery hatch are held down with earth magnets. The only other alteration I made was to change the landing gear mount from solid hardwood blocks to built-up plywood assemblies. This was done for those modelers who don’t have a small saw to do the slotting work. The airframe is self-aligning sheet wood with everything included in the short kit but the hardwood blocks and hardware.Wing
The wing construction evolved from a traditional method of slotted LEs and TEs to a more modern version using all laser-cut parts. Cover your plans with wax paper and pin the lower spar to the plans. If you can’t get hard balsa, use basswood because the strength is worth the slight weight gain. Fit R-1, R-2s, R-3s and R-3T over the lower spar and into false TE notches. (Note R-3T is slotted to accept the wingtip former.) Ensuring the ribs are aligned to the plans and perpendicular to the spars, pin them to the building board. Glue them to the lower spar and notched false TE using thin CA. Glue the top spar to the ribs and install the notched false LE. If using the short kit, the bevel for dihedral is already cut and you need to correctly position it. Install 1/8-inch LE and 1/4-inch TE. Install 1/16-inch plywood R-2As, with the 3/32-inch sheer webbing centered between the upper and lower spar. The grain should be vertical or perpendicular to the spar grain. Install the aileron servo mounting plates. Tubes to route aileron servo wires are made up of scrap paper and glued between R-1 and R-2 prior to joining the wing halves and planking the center section. Shape the LEs and TEs using a razor plane and sanding blocks. Glue the wingtip formers to R-3T. Glue the wingtip braces R-5 through R-8 to the top and bottom of the wingtip former—this will require bevel sanding for proper fit where the braces meet R-3T. Glue a set of T-1, T-2, and T-3 to the top and bottom of each wingtip. Glue T-9 to the top and bottom of each wingtip. Shape the wingtip with a razor plane and sanding blocks.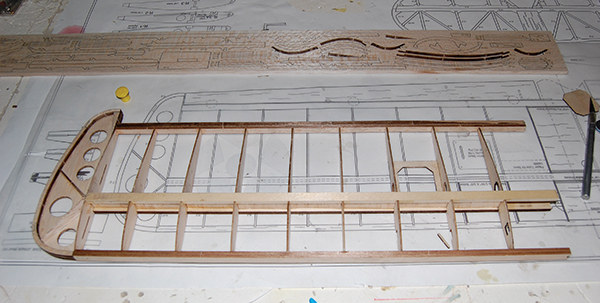
Build up a left and right wing panel over the plans. The panels are joined with plywood doublers.
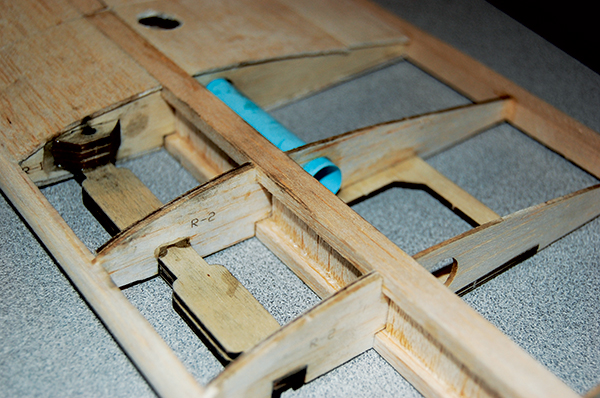
The landing gear blocks can be cut from hardwood or built up from plywood.
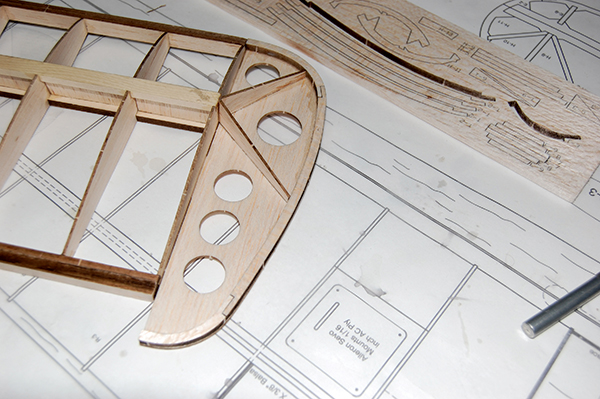
The wingtip can be built up on the wing or assembled and added to complete it.
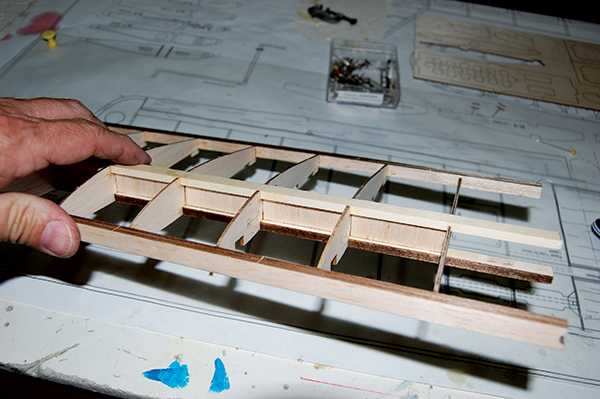
I do my capstrips as I-beams, but other methods can be used. Don’t leave them off and be sure to make the grain perpendicular to the spar to strengthen the wing. The wing panels are joined with epoxied 1/8-inch plywood doublers. Install the 1/8-inch center rib to allow for 1/16-inch planking. Place scrap balsa on both sides of the center rib to provide material for wing-dowel mounting. Install 1/16-inch square stock across the LE spar and the TE to give the center planking something to adhere to. Plank the center section using 1/16-inch balsa. Install a 3/16-inch dowel in the wing’s center. To install the landing gear blocks, build up the left and right landing gear block assemblies by gluing two L-2s to an L-1 with spacing for the 1/8-inch music wire. Glue two sets of three L-3s into a stack and attach to R-1. Use epoxy to glue the landing gear blocks to the L-3 stack and ribs. The main landing gear is bent from the music wire and held in place with tin straps and servo screws.
Fuselage
Pin one fuselage side assembly flat on the building board and install F-3, the battery compartment floor, the wing hold-down bracket, and F-4. Ensuring that the fuselage is not twisted, install a second fuselage side. Pull the side formers together and install F-2. Build up the motor mount and nose block by using epoxy to glue two F-1s with F-1A through F-1C. Install the nose block/motor mount assembly with epoxy. Glue in F-5 through F-8. Ensure that the fuselage is symmetrical and not twisted, bring the two sides together, and glue them at the rudder post. Glue in ¼-inch triangular stock along the lower fuselage sides between the wing mount and the rudder post and between F-2 and F-3. This triangular stock provides support so that the lower fuselage sides can be rounded at the corner. Using 3/32-inch balsa planks, plank the fuselage top between F-2 and F-3, and plank the lower fuselage between F-2 and F-3 with 1/8-inch balsa sheet. Plank the lower rear fuselage with 1/16-inch balsa. Glue in 1/16 x 1/8-inch balsa or basswood stringers on the turtleback. Shape the bottom edges of the fuselage. Using 1/4 balsa sheet, build up the top and bottom areas between F-1 and F- 2 with balsa blocks. Do not glue these. Shape the nose blocks and the bottom and top hatch blocks. To expedite the process, use a power disk and belt sander to rough sand the area into shape. Hollow the upper and lower blocks to a 1/4-inch thickness. Using epoxy, glue the bottom block between F-2 and the nose blocks. This block is critical because it carries motor stress back into the fuselage. Add guide blocks to the bottom of the upper block to align it with the fuselage sides. Install the rudder and elevator pushrods. Glue 1/16-inch x 1/8-inch balsa stringers to the turtleback. On a flat surface covered with wax paper, glue the hatch skin. Glue the three F-3As to the battery hatch base, then glue four 1/16 x 1/8-inch stringers into the notches in the F-3A formers. With the battery hatch base on the edge of a table, beginning at the centerline, hold down one side of the hatch skin, allowing the excess to hang over the table as you glue. Trim the excess skin off, allowing the hatch to rest flat on the table surface, and then glue the other side. Add scrap balsa strips to each side of the hatch base to align it with the fuselage sides. Cut out the cockpit openings.Tail Surfaces
These are built over the plans. Cover the horizontal and vertical fin prior to mounting them on the fuselage. The area where the vertical fin meets the horizontal stabilizer is filled in with balsa blocks and covered in blue after they are installed.Covering
The various prototypes have been covered with everything from Solarfilm to EconoKote. A slight weight savings is an advantage of this type of film covering, but does not affect its flying abilities.Final Assembly
The motor is an E-flite 450 outrunner and is used with a 10 x 5E or 10 x 7E APC propeller. It is rated for 14 amps for Scale models in the 30-ounce weight range. Any motor in that range should work. Power is managed with a Castle Creations Thunderbird 18-amp ESC connected to a 1,650-2,000 mAh LiPo 3S battery. Mine are from Common Sense RC. The motor current is set up using an Astro-Flight watt meter at 10-12 amps static using the ATV function on the transmitter. I used a Futaba 8U transmitter linked to a four-channel Berg receiver. Two Hitec HS-81 servos control the rudder and elevator, and two Hitec HS-55 servos work the ailerons.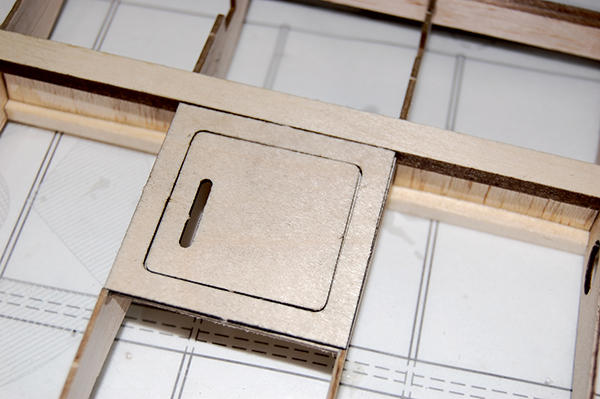
I made the aileron servo mounts out of 1/16-inch aircraft plywood.
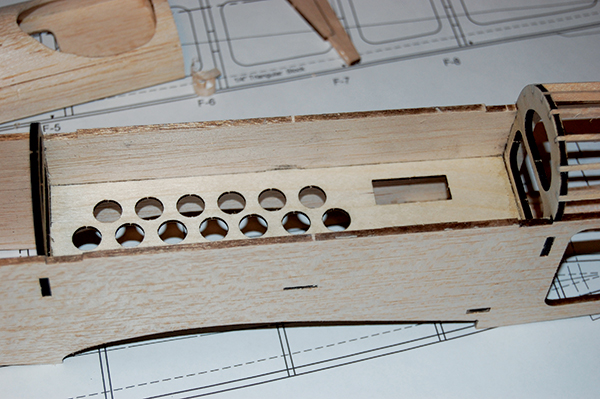
The plywood battery compartment floor is perforated to allow air to circulate, and the cockpit openings allow heat to escape. The receiver and rudder and elevator servos are mounted to the battery compartment floor, with the aileron servos mounted in the wings. Du-Bro aileron linkage and park flyer pushrods are used throughout. I chose E-flite wheels. The mains are 21/2-inches in diameter with a 3/4-inch diameter wheel on the tail.
Flying
Similar to Bob’s original glow version, my electric PT-19 is a pleasure to fly. It is the one model that I can say flew right off the building board. If I had to compare it with anything in the commercial market I would say it is most similar to the Sig Four-Star. The first flight was out of a parking lot, but with 2- or 21/4-inch wheels it will fly off short grass. The PT-19 is not twitchy when airborne and tracks straight with good response. Elevator throws should be limited to the 3/8-inch range for the first few flights.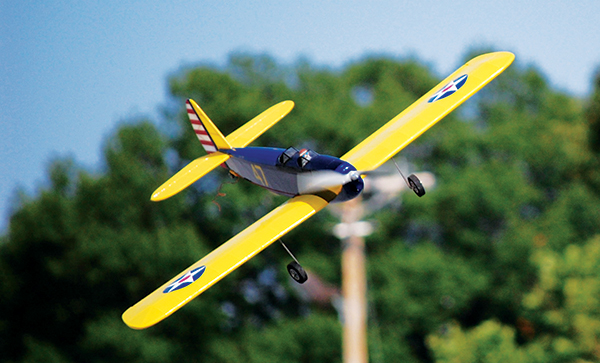
The PT-19 is not twitchy and tracks straight with good response.
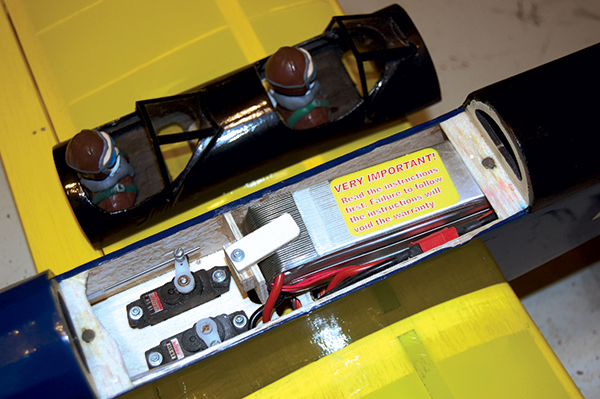
Turnaround time between flights is less than a minute because the hatch simply lifts off. The battery can be quickly swapped. It is a true sport model that can perform aerobatics with ease. Large loops, inverted flight, stall turns, snap rolls, aileron rolls, and spins are a breeze. With the 2,000-mAh flight packs, and my flying style (half to three-quarter throttle), flights are approximately 15 minutes, leaving the battery warm to the touch upon landing. At a weight of 25 ounces, it is best in light air but can easily handle midafternoon breezes. Turnaround time between flights is less than a minute because of easy battery compartment access. To land, keep the nose down and carry a little power on approach. Flare holding the nose up and let it settle. Its wide gear and long tail make takeoffs a breeze. It tracks straight with no tendency to swing on takeoff. If you use the 450-sized motor, it only needs roughly 20 feet of runway. Everywhere I take it people ask me which company manufactures it and I get to tell them it is scratch-built. The pride that comes from that would make it difficult for me to go back to ARFs.
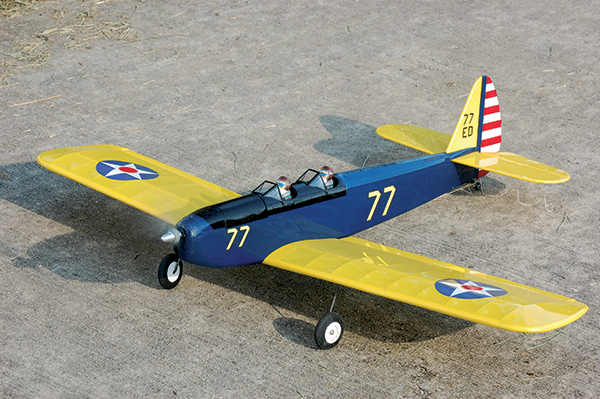
Vinyl graphics from Callie Graphics provide a complete and finished look. Thank you to Callie Graphics for the custom decals and John Valentine of Top Notch Product Company for the short kits. —Charles S. Pipes [email protected]
Bonus Photos
Download Free Plans
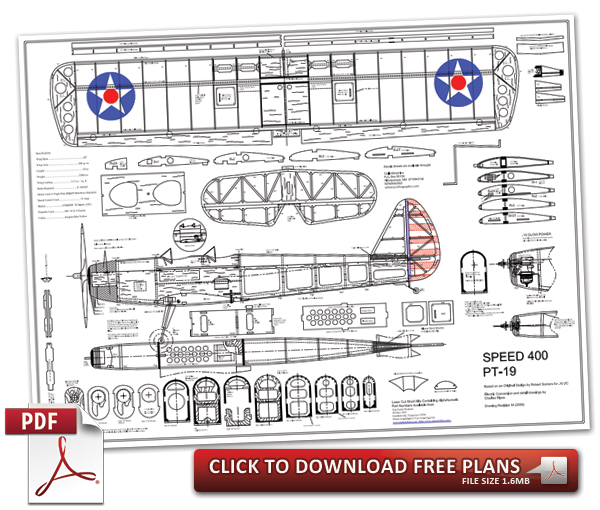
Or visit www.modelaviation.comhttps://modelaviation.s3.us-east-2.amazonaws.com/PT-19Speed400.pdf
Download Free Builder's Guide
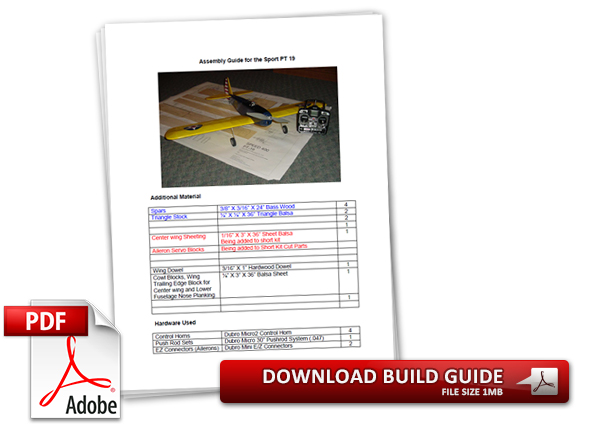
Or visit www.modelaviation.comhttps://modelaviation.s3.us-east-2.amazonaws.com/PT-19-Builders-Guide.p…
Specifications
Model type: Semiscale electricWingspan: 40 inches
Weight: 22-26 ounces
Wing area: 300 square inches
Wing loading: 12.5 ounces per square foot
Power system: E-flite 450 outrunner; 18-amp ESC; 1,650-2,000-mAh 3S LiPo
Radio: Four-channel with four microservos
Test-Model Details
Motor: E-flite 400-450 brushless outrunnerSpeed control: Castle Creations Thunderbird 18-amp brushless
Propeller: APC 10 x5E or 10 x 7E
Battery: Common Sense RC 1,650 or 2,000 mAh 3S LiPo
Transmitter: Four-channel
Receiver: Four-channel or above
Servos: Hitec HS-81; Hitec HS-55
Tail wheel: E-flite .75 inches
Main wheels: E-flite 2-2.5 inches
Sources
Top Notch Product Company(615) 866-4327
www.topnotchkits.comE-flite
(800) 338-4639
www.e-fliterc.comCastle Creations
(913) 390-6939
www.castlecreations.comHitec RCD
(858) 748.6948
www.hitecrcd.comCommon Sense RC
(866) 405-8811
www.commonsenserc.comCallie Graphics
(505) 281-9310
www.callie-graphics.com
Comments
Great
Great
Questions
My email is in the article and I will more than glad to field questions for anyone that decides to build it.
Hope everyone enjoys flying this as well as I have.
how it flies
How does this compare with the electric 40 inch wingspan Super Sportster. It seems like it might fly in a similar manner. Looking for your response. Thank you. I have ordered the short kit. It will be my first build. I have a friend who is a long time model builder who can help me.
How it Flies
I have never flown a Super Sportster, but will say that it flies like a Sig Four Star does. It flies pretty much like any model with a long tail and a light wing loading.
I lost my vision to the point where I should have quit flying right after I built the PT-19. I flew for a couple of years more and finally gave it up three years ago as my sight got worse. I have had lense replacement surgery and can now fly again.
Went out Monday and flew seven flights with it , all about fifteen minutes each. Flew with a friend that had not flown in ten years and we had a great time. We both agree it is a great plane to learn on. It will do all the basic aerobatics, and with a 450 out runner, climb just about vertically. Having lost our flying field for gas models, we take our electrics to the local church yard.
Anyone that is interested can send me an email to [email protected] and I will send you extra build along photos and a short (Unfinished build along article) that may help with the motor mount system I used.
Charlie Pipes
enlarging to 60 inch wing span
Been looking for a kit or plans for a larger pt-19. Thinking about enlarging to a 6o inch
wing span. Do you see a problem in doing this? Also if i could get the motor installation
instructions if you have them available. Also does the opening in the cowl give
sufficient cooling for motor and esc.
thanks in advance.
jim
How it Flies
This is my second attempt at a reply so you may get two answers. I am not sure about the password system at the bottom.
I have never flown a Super Sportster but will say the PT-19 does fly like an electric version of the Sig Four Star series.
Send me an email to [email protected] and I will send you the build along that I started and extra photos.
Charlie Pipes
wing didedral
Do you know how much dihedral is in the wing.
tail spar thickness
can you please tell me about tail spar thickness and other dimension?
I enlarged the plans to a 60
I enlarged the plans to a 60 inch wing span. My original idea was to build up the
Fin and rudder pretty much according to the plans. The more i thought about it,
the plans were just too figgety, and just cut the fin and rudder out of 1/4 inch balsa sheet.
Alot less trouble, with not much of a weight penalty. If you are building the original
40 inch version I would just cut them out of 3/16 or 1/4 inch balsa and be done with it.
Extra Help for Builders
Should anyone wish extra help in building I will be glad to send a short Build A-Long article that is a little more step by step. I will also send extra photos that were not in the Magazine or here.
[email protected]
Charlie Pipes
Radio Control Zone Forum
If you go to the link below it will take you to the original Builders forum on the PT 19 thru all its versions.
http://www.radiocontrolzone.com/showthread.php?t=232865
scratch building 60 inch wing span
In process of scratch building 60inch wing span based on original plans. So far so good.
made kit by making tempates from 1/4 inch foam board. This method seems to work very well. Easy to trace
parts onto balsa and ply. This my first attempt at a scratch built, and am pleased with the quality of
the plans and the building instructions. Looks like a well designed plane. Plan on using a .32 electric
motor. Hav,nt decided yet on how to mount motor. May build up a firewall behind cowling and mount
motor via a motor mount. That is down the road, as I am still working on the wing.
contemplating adding flaps. If you are looking for a first scratch built project, this may be a good
starting point.
g templates
additional advice on building wing.
The only real problem I have encountered building wing is attachment point of ribs to leading
and trailing edges. I had problems making notiched false leading and trailing edge spars. To get around
this, I used 1/8 x 3/4 bass wood for the false leading edge and 1/8 x 1/2 bass wood for the t
false false trailing edge. I then used 1/4 x 3/4 balsa between alternate bays, glueing to the false leading
edge, and to the ribs. For the trailing edge, I used 1/4 x 1/2 balsa between alternate bays glueing
to the false trailing edge, and the ribs. This seems to have made a very strong bond, with a very
small weight penalty. I am sure there are many other methods, but this seems to have worked
for me.
update on wing
The scratch built 60 inch wing is just about complete. Something I would do differently
were I to build another. I would eliminate the 1/8 basswood leading and trailing edge false spars
as these are probibly overkill, and just add weight. The reinforcements between alternate bays
are more than suffiecient to add strength. I am also debating whether the bass wood main
wing spars are necessary, and wonder if balsa spars would be suffiecient, although For a
first scratch wing I am erring on the side of caution. the wing is coming out a little bit
heavier than I would have liked. I am going to use a emax gt_3220/4 for power . The reason
I chose this motor is dimentionally it fits perfectly with the enlarged plans. I am hoping it is
strong enough to carry the increased weight of the wing. We will see. I am hoping to come in
at around 5 pounds with the complete plane.
Onward with the construction with the fuseledge.
done differtly if I were to bjild
starting fuselege of pt-19.
I,ve started the fuseledge of the pt-19.
After creating tempates from 1/8 foam board, I traced the forms to 3/32 balsa and 1/8 lite ply.
I have used 1/8 lite ply for the fuseledge sides and the battery compartment floor.
Formers f2, f3, and f4 are 1/4 inch lite ply made by laminating two of each former together.
the engine mount was made by laminating 3 of these formers together, creating a
3/8 inch motor mount. I have debated mounting the motor by mounting the it to a fire wall
at the rear of the motor, but think the method shown on the plans and the building guide
will work.
I have also decided to use a different motor. I originally thought the emax gt-3520/4 would
be suffient, however, given the added weight of the wing, I have decided to upgrade
to the emax gt-3526/5. I feel the original motor may have been suffient, but marginal.
Using the larger motor I will have the option to use a larger prop, but will require a
more robust esc. Probibly a 80 amp. Also the deminsions are almost identical to the
the smaller motor, with the diameter is the same, allowing me to use the same motof
mount shown in the plans.
If you have never done a scratch built, try this one. I am pleased with result so far.
onward with the fuseledge.
jim
So far the build has gone quite well, with no major issues.
As I said
tail spar thickness
Can anyone please tell me about tail's spar thickness and other dimension ??
tail spar dimemsions
I am building a enlarged 60 inch wing span version of this aircraft. I used 1/4 x 1/2 bass wood
for extra strenth of the tail spar. If you are building the 32 inch original version I would
probibly go with 1/4 x 1/4 basswood, if using balsa I would probibly go with 1/4 x 1/2 .
Just suggestions.
jim
changed engine mounting method.
I changed my minc on how to mount motor. I made s engine bulkhead by laminating 1/8 plywood
creating 1/4 Inch bulk head (f1 and f2 formers laminated). I then attached motor , a emax 3026/5,
Behind this assemhly by attaching included motor mount to front of motor. And drilling holes through
bulk head and attaching engine mount behind bulk head by running 3/4 inch machine screws through
front of bulk head , through mounting holes in engine mount, and securing with blind nuts behind
engine mount. This allows me to replace or remove motor if necessary. I will devise a way to make
top hatch over motor removable.
g
by mounting
HmBQS
Hello there! I know this is kinda off topic but I was wondering which blog platform are you using for this website? I'm getting fed up of Wordpress because I've had issues with hackers and I'm looking at alternatives for another platform. I would be awesome if you could point me in the direction of a good platform.
motor hatch construction
Made motor hatch very simply. I made another F3 former out of 1/8 inch lite ply.
I then cut this in half to come down to height of fuseledge. I then glued this to front of F3 former.
Thes gives the rear of engine hatch something to sit on. I then glued 1/8 ply wood strips
to the inside of the fuseledge at the hatch opening extending 1/2 inch above the bottom
of the hatch opening. This gives the bottom edge of the hatch something to attach to.
then wrapped the wet balsa hatch over the extended F3 former and over the top of motor fire wall.
I trimmed the bottom of the hatch flush with the top of the fuseledge and pinned the bottom of
the hatch to the ply wood strips glued at the bottom of the hatch opening.
After this part dries it will retain the shape of the hatch formed by the F3 and firewall.
It then was simple to glue 1/8 × 1/2 inch lite ply strips to the bottom of the hatch sides,
for attachment reinforcement. I then coated the inside the hatch with 5 minute epoxy
to strenthen the hatch and after it had cured attached the hatch by screwing it to the
fuseeledge with sevo screws running through bottom of the hatch and into the 1/8 plywood
attachment strips at the bottom of hatch opening glued earliar.
Makes a strong but light weight removable hatch for the motor.
i
f the
I
I then cut 3/32 balsa to approximate shape of hatch opening. After soaking this part in hot water
for approximately 5 minutes, i wrapped the part around the additional F3 And the engine
fire wall. I trimmed the bottom of the hatch flush with top of the fuseledge.
Extra Help for Builders
Extra Help for Builders
Should anyone wish extra help in building I will be glad to send a short Build A-Long article. I will also send extra photos that were not in the Magazine or here.
[email protected]
Charlie Pipes
Email not work please if you glad to send me on email [email protected] short Build A-Long article.
THANKS
PT-19 printer version
Purchased two short kits from Top Notch Models - Nice; hope to try out in the
spring (if winter ever leaves Northern New England).
60 inch wing span conversion
This. Was my first scratch built project and enlarged plans to 60 inch wing span.
Build was stteight foreward with very few problems. Plane flys like a dream with only
Adjustments needed was additional nose weight, beefing up landing gear attachment points
And slight up elevator trim. If you have never tried a sctatch build, try this one.
You won,t be sorry.
Jim
Pyj
EZ FAIRCHILD PT-19 Build Manual
Hello,
I just got a EZ Fairchild PT-19 RC plane, however I have not found the assembly manual... can you help to get this?
This was manufactured by Sports Aviation CO.,LTD
Thank you
Gostaria de fazer PT 19. Pois
Gostaria de fazer PT 19. Pois já vi voar. Já fiz um Monet 162 com um motor 15 Cox e um Stuka de fuselagem 1,30cm motor 60 Fox. Obrigado
Sou Aeromodelista faz 60 anos
Sou Aeromodelista faz 60 anos, moro em Bauru São Paulo. Já construi quase todos tipos de aeromodelos. Desde elástico,,Tean Racing,planadores, Rcp, mais o que eu gosto é construir asas de Combate. Último aeromodelo construído foi Monet 262, só que.modifiquei, de vez de ser de turbina, coloquei um Cox 15, é para VCC. bF9
Add new comment