Written by Louis Joyner
As featured on page 125 in the November 2011 issue.
MATERIAL CHANGES: For at least 80 years, balsa has been the material of choice for hand-launch gliders. But, just as the event has dramatically changed from the traditional javelin launch to tip launch, construction materials and techniques are also starting to change.
Javelin-launch gliders typically measured 16 to 22 inches in wingspan and weighed roughly an ounce. Models were also considered somewhat expendable. Serious fliers produced large batches of gliders knowing that some would be broken, some wouldn’t fly well, and others (always the good ones) would be lost in thermals. Because it is readily available and easily worked using simple tools, balsa was the perfect material choice for these disposable models.
However, the new tip-launch gliders are much larger, typically with a wingspan from 30 inches up to the maximum of 1 meter (39.37 inches). The weight is triple that of a javelin-launch glider. With the nearly universal use of a DT, flyaways are greatly reduced. Consequently the tip-launch gliders last longer, allowing more time and money to be invested in construction. This also means that models can be more accurately constructed.
Although balsa is still a viable choice for larger tip-launch models, some modelers are exploring other options for wing construction. Although the choices vary in the materials and building techniques used, they all utilize a stressed-skin structure.
Unlike a solid balsa wing, a stressed-skin structure uses two different materials, each to its best advantage. The top and bottom surface “skins” provide the bending and torsional strength; the lightweight core provides the airfoil shape and keeps the top and bottom skins apart under bending loads.
Stressed-skin structures are nothing new in modeling. Many RC models utilize a foam core covered with thin-sheet balsa or even heavy plastic film. Others use fiberglass, aramid, or carbon fabric to handle thinner airfoils and higher flight loads. In FF, wings sheeted top and bottom with thin balsa have been used for years. Closely spaced balsa ribs provide the core function.
More recently, thin, hard aluminum foil, fiberglass cloth, or carbon fabric have provided the stiff outer skin, either over a fully sheeted wing or a foam core. In principle, even a traditional stick-and-tissue wing is a stressed-skin structure, with the taut tissue adding both bending and torsional strength to a lightweight balsa framework core.
The Core: For tip-launch gliders, the most popular core choices are insulation foam, Spyder Foam, and Rohacell foam. Pink and blue insulation foam is available at most home stores in 4 x 8-foot sheets in a variety of thickness.
Although inexpensive and readily available, these are not the best choices among insulation foams, because the compressive strength is quite low—typically 15 to 25 pounds per square inch (psi). For a core material, compressive strength is one of the most important attributes.
Specialized insulating foam, designed for certain commercial applications, has at least twice the compressive strength. Dow Styrofoam Highload 60 insulation, has a compressive strength of 60 psi and a weight of 2.3 pounds per cubic foot (pcf). The sheet size for the pale blue material is 2 x 8 feet in both 2-inch and 3-inch thickness.
Dow also offers slightly lighter Highload 40 with a 40 psi compressive strength in both 2 x 8 and 4 x 8 sheets and 2- and 3-inch thickness. Cost for a 2 x 8 sheet of 2-inch material should be less than $25, provided you can find a local dealer that stocks it. (In my town, the Highload foam is a special order item with a three-pallet minimum; I didn’t bother to ask the price.)
Owens Corning offers a similar product. Foamular is high compressive strength rigid foam that is pink in color. Foamular 600 has a 60 psi compressive strength and a weight of 2.2 pcf; Foamular 400 has a strength rating of 40 psi and weighs 1.8 pcf.
Spyder Foam, also known as surfboard foam, is extruded so that its maximum compressive strength is in thickness, just where it is needed for a wing core. Spyder Foam has similar strength and weight characteristics to Highload 60, with a weight of 2.3 pcf and a compressive strength of 60 psi. Formerly available in white, Spyder Foam now comes in blue.
The Composites Store (CST) stocks Spyder Foam in 1.75-inch thickness; a 12 x 36-inch sheet is $15.95 plus shipping; a 24 x 36-inch sheet is also available for $27.95, but there is a $20 packing charge and an oversize shipping charge for the wider sheet. According to Gail Gewain of CST, the manufacturer discontinued production of Spyder Foam in late July. After the current stock is gone, it will no longer be available.
The foams I’ve mentioned are extruded polystyrene foam (EPF). The next foam choice is Rohacell, a white, closed-cell acrylic foam. Unlike polystyrene, Rohacell cannot be hot-wired. It must be machined or sanded to shape.
Rohacell industrial grade (IG) foam comes in three weights: IG 31 (2 pcf) with a compressive strength of 57 psi; IG 51 (3.2 pcf and 128 psi); and IG 71 (4.7 pcf and 213 psi). Rohacell is widely used in the industry as a core material for such things as wind turbine blades, helicopter rotors, and even hockey sticks.
Rohacell IG 31 is available from CST in 3.0mm, ¼ inch, and ½ inch thickness, and in a range of sheet sizes. IG 51 comes in the widest thickness range: 1.0mm, 1.5mm, 2.0mm, 3.0mm, and ¼ inch. IG 71 is offered in 3.0mm, ¼ inch, ½ inch, and 1 inch. As with the Spyder Foam, there are extra charges for sheets wider than 12 inches. Rohacell also offers IG-F, which has a finer cell structure for reduced resin absorption. CST is starting to carry IG-F in some weights and thicknesses.
As a core material, Rohacell offers higher ratio of compressive strength-to-weight than EPF. Rohacell IG 51 has double the compressive strength of Highload 40 (128 psi compared to 60 psi), but only weighs about 1.4 times as much. Rohacell also resists temperatures up to 428 F (220 C), an important consideration for models that often sit in the sun. The maximum use temperature recommendation for one major brand of EPF is only165 F (74 C).
“Rohacell is really hard to beat when you look at all the properties,” said Gail. But the good qualities do come at a price. A 12- x 48-inch sheet of ¼-inch Rohacell is almost $60, or roughly $20 per tip-launch glider wing.
Shaping the Core: For EPF foam cores, the easiest solution is to use the hot-wire technique. The basic idea is to cut the wing panel to outline shape, attach airfoil-shaped templates to both ends, then use a heated wire to cut through the foam, following the templates.
The main limitation is that the wire only cuts in a straight line, so panels need to be rectangular or trapezoidal in shape. However, by using a six-panel wing and tapering each panel, you can approximate an elliptical planform. The tips can be sanded after hot-wiring.
Since Rohacell foam can’t be hot-wired, it must be sanded or machined to shape. Sanding actually goes much faster than with balsa. As with balsa, a vacuum and face mask should be used to control the dust. Rohacell also cuts easily with a saw or router. For faster and more accurate production, a jig could be devised to hold a router at the correct angle to shape the sloping rear of the wing airfoil.
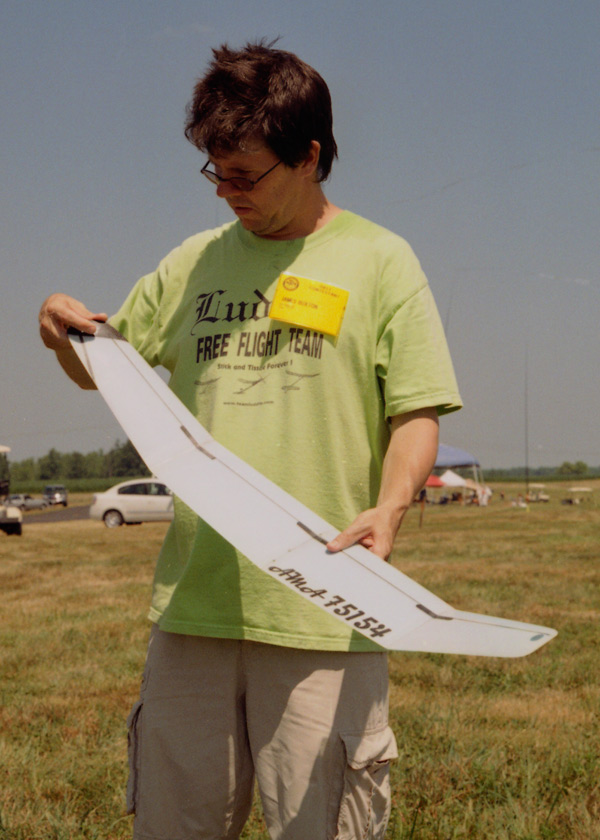
Jim Buxton's tip-launch glider sports an insulation foam wing, skinned with two layers of lightweight glass cloth. Its projected wingspan is slightly less than the l-meter maximum.The Skin: Possible choices for the skin include fiberglass cloth, carbon-fiber cloth, and carbon tissue, also known as carbon veil. Lightweight fiberglass cloth is familiar to most modelers. The silklike material comes in weights as light as ½ ounce per square yard. When using fiberglass or carbon cloth, it is best to use a cloth with a balanced weave, one with the same number of threads per inch in both directions such as 0.7 ounce fiberglass cloth with a 56 x 56 thread count. This will ensure equal strength in both directions and minimize the chance of warping. Handling light fiberglass cloth isn’t easy, but carefully unfolding the cloth onto a smooth surface such as a large piece of illustration board or brown wrapping paper will help reduce snags. Smooth it out with gentle strokes of a drafting board brush, then mist with clear nitrate dope. This will lock the threads of the cloth together, stiffen it slightly, and make it easier to handle. Carbon-fiber cloth comes in a variety of weights; the most usable for FF are approximately 2.25 to 2.9 ounces per square yard. Carbon cloth is considerably stronger and a good deal more expensive then fiberglass cloth. As with fiberglass cloth, carbon fabric is almost always used on the bias, that is, with the threads running at 45° to the wing chord. This provides a significant increase in torsional strength as opposed to a chordwise/spanwise fiber orientation. Many of the same handling techniques used for fiberglass cloth are needed with carbon fabric. It helps to use drafting tape to outline an area of the cloth and then cut along the center of the tape. This will minimize the chance of the fabric unraveling or pulling out of shape. Another alternative to fiberglass or carbon cloth is carbon tissue. Instead of being a woven cloth, carbon tissue is a thin mat of random fibers. Just imagine black silkspan. Available weights range from 0.2 to 0.7 ounces per square yard. No special handling is required; simply cut to shape with scissors. The costs of fiberglass cloth and carbon tissue are comparable, in the range of $16 to $18 dollars a square yard for carbon tissue, perhaps slightly less for light glass cloth. Carbon-fiber cloth is expensive—roughly $150 per square yard and more for lighter cloth. For certain applications, the added strength, rigidity, and dimensional stability are worth the cost. Bagging It: Attaching the skin to the top and bottom of the core is the easiest part of the operation. The cloth or tissue pieces are placed on a piece of thick Mylar and wetted out with epoxy resin, and then the excess resin is blotted off. Next the core is positioned over the bottom skin and then the top skin placed on top of the core. Another piece of Mylar is draped over the assembly, and everything is placed inside a vacuum bag. The bag is sealed and a vacuum pump is used to remove the air from the bag. Atmospheric pressure does the rest, evenly pushing the skins tight against the core. The vacuum is held until the epoxy hardens. The result is a stiff wing that won’t flutter on a hard launch and won’t change between contests. More importantly, you can make another one just like it without spending weeks searching for a perfect piece of balsa. Matt Gewain has created an excellent tutorial about vacuum bagging, which can be seen on the CST website. Other websites offer tips, instructions, and even how-to videos. Is it worth it? Composite glider wings require an investment in both time and money, as does any new technology. For some of us, the feel of a razor-sharp plane on a piece of C-grain balsa offers more rewards then messing with epoxy and strange plastics. For others the challenges of trying something new may be its own reward. Neither the thermal nor the stopwatch care how the wing was made or what materials were used.
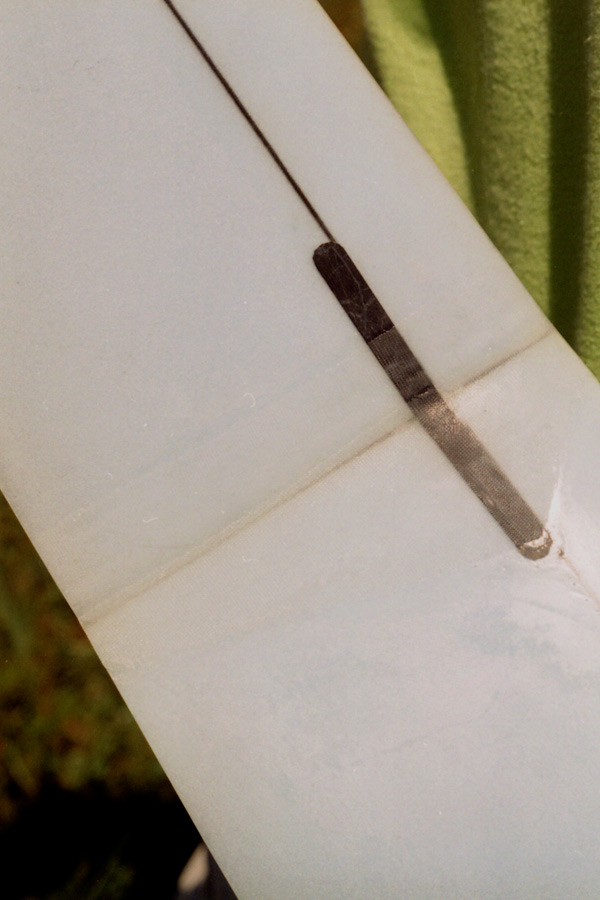
Narrow carbon-fiber spars on the top and bottom stiffen Jim Buxton's glider wing. Each dihedral joint is reinforced with carbon tow.I had the opportunity to examine two composite-wing gliders at the Nats last summer. The wing on Jim Buxton’s model used cores hot-wired from blue foam and skinned top and bottom with two layers of 0.7-ounce fiberglass cloth. For added bending strength, Jim inset 0.050 inch carbon fiber spars into the top and bottom of the core before adding the skins. A simple tool made from a broken Dremel cut-off disc with scrap-balsa depth stops glued on either side was used to cut the groves for the carbon spars. “It’s quick and easy,” said Jim. Dihedral joints were reinforced with carbon-fiber tow on the top only to reduce bending on launch. “It’s scary how flat these high-aspect-ratio wings get on launch,” he adds. The four-panel wing measures 42 inches flat; dihedral reduces the span to within the 1-meter maximum allowed by the rules. Root chord is 5.5 inches tapering to 4.375 at the break and 3 inches at the tip. Because of the taper, each of the four panels was cut out individually from the foam, then the airfoil hot-wired. The tips were rounded off by hand using sandpaper. West Systems laminating epoxy resin was used to apply the fiberglass skin. Total weight of the 175-square-inch wing was 66 grams. Out of curiosity I estimated component weights on Jim’s wing. The foam core was roughly 18 grams, the four layers of fiberglass cloth totaled approximately 16 grams, and the epoxy another 16 grams (ideally the weight of the epoxy used should equal the weight of the cloth), totaling roughly 50 grams. The carbon-fiber spars, carbon-tow reinforcements, extra epoxy at the dihedral joints, and the shark fin throwing peg added the rest. Calculating the skin weight is easy and accurate, but determining the exact volume of the core is more difficult. My guess could have been off 10% or more either way. Although a 50-50 ratio of epoxy to cloth is ideal, it can be difficult to achieve. In this case the epoxy weight could have easily gone above 20 grams. With any type of construction, keeping accurate weights of each part as you build is important. The other glider I examined was British glider flier Mark Benns’ Spin-Up 1000. This is the follow-up design to his balsa wing Spin-Up. (A kit for the balsa version is available from A2Z Corp.)
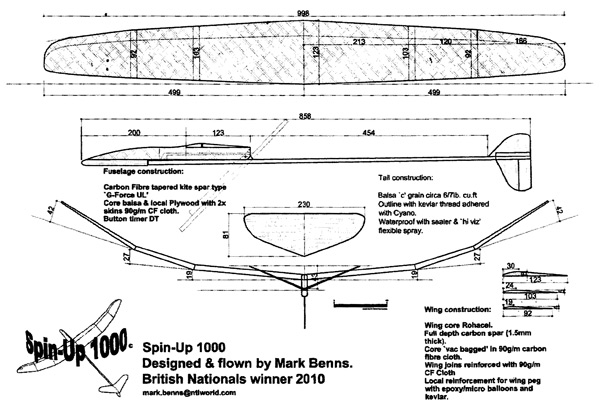
The new carbon-wing Spin-Up 1000 was selected as a British Model of the Year, featured in the 2011 Free Flight Forum, and reviewed in the August 2011 “Free Flight Duration” column.The wing for the Spin-Up 1000 utilizes a Rohacell IG-F 51 core skinned with 90 grams per square meter (roughly 2.6 ounces per square yard) carbon cloth. The core was machined to the exact shape using a CNC (computer numeric control) milling machine fitted with a 1mm end mill. Once programmed, the mill precisely shapes the wing outline and airfoil. “I come back in an hour and it’s all done,” says Mark. Using a CNC mill allows the wing core to be cut as a single piece and also permits a curved planform.
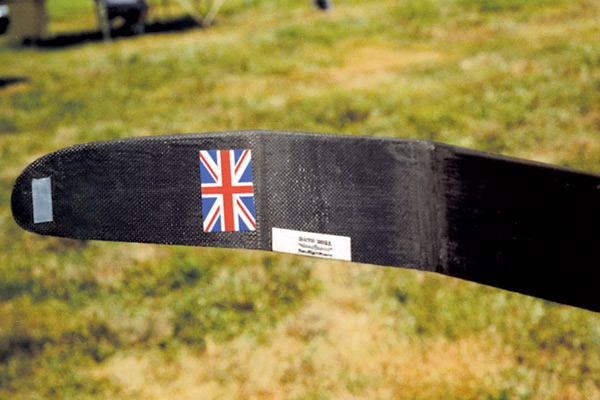
Carbon-fiber cloth is oriented on the bias for maximum torsional stiffness. A carbon I-beam spar in the core provides bending strength.Before skinning, a full-depth spar of 0.7mm carbon fiber is added then carbon caps are added top and bottom to create a stiff I-beam spar. Carbon tow placed along the LE adds extra strength and ding resistance. Then the carbon cloth skins are wetted out with epoxy resin, placed on the core, and the wing vacuum bagged.
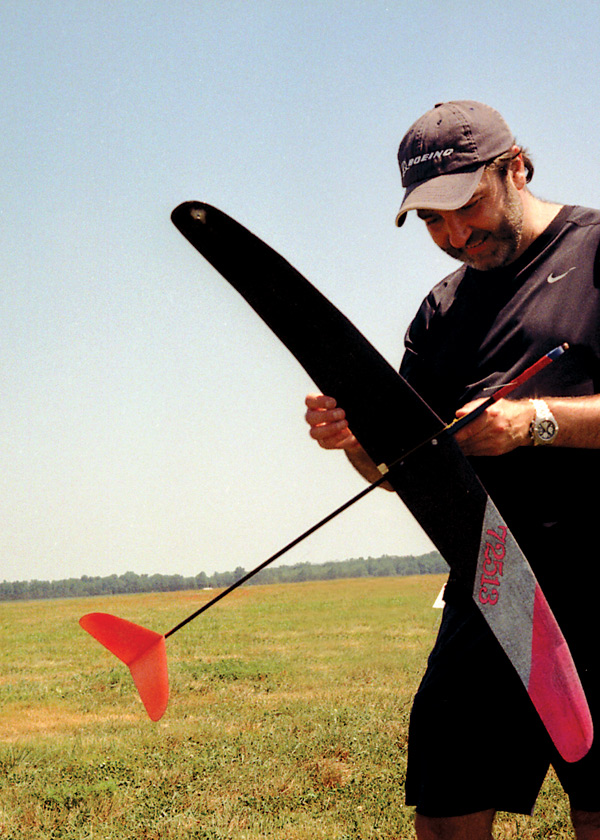
Designed for windy weather, Mark's Spin-Up 1000 glider features a wing skinned with carbon-fiber cloth over a Rohacell foam core.My calculations put the wing area for the Spin-Up 1000 at approximately 152 square inches. I estimated the core weight at between 20 and 25 grams, the carbon fiber cloth weight at slightly more than 18 grams, the epoxy weight at 18 to 20 grams, and the carbon-fiber spar at roughly 6 grams. That’s a total of 62 to 69 grams for the wing—surprisingly close to Jim Buxton’s wing weight of 66 grams. If you are accustomed to the old javelin-launch balsa gliders, a 2.25-ounce wing may seem heavy, but Mark’s model is designed for windy weather with an all-up weight of 90 to 110 grams. On the plans, Mark suggests an alternate wing construction employing 10 pounds per cubic foot balsa. A 4- x 36-inch sheet of 5/16-inch thick balsa weighs approximately 120 grams and has an area of 144 square inches—slightly smaller than the Spin-Up’s area. Even if half the sheet of balsa is planed and sanded away to make the wing, the weight would be 60 grams without a finish and the necessary reinforcements at dihedral breaks and throwing peg.[dingbat] Sources: CST-The Composites Store
(800) 338-1278
www.cstsales.comNational Free Flight Society
www.freeflight.orgDow Building Solutions
(866) 583-2583
www.building.dow.com/na/enOwens Corning
(800) 438-7465
www.foamular.com/foamEvonik Industries
rohacell@globaloffice
www.rohacell.comA2Z Corp.
(877) 754-7465
www.a2zcorp.us
Comments
Wing Launch Glider
Many thanks AMA for your excellent article on the Spin-Up 100 and new materials - intelligent - informative - complete
thanks :0
thankyou you helped me with my glider assignment
Howmuch
Howmuch
Rohacell hot wire
Rohacell like other acrylic foam (Cascell) can be cut perfectly with hot wire. All my F1A wing cores are cut that way. Just enter 'Rohacell hot wire' in Youtube for the result.
Add new comment