Written by James Wang
RC Helicopters
As seen in the Ocotober 2020 issue of Model Aviation.
WELCOME TO THE "RC HELICOPTERS" COLUMN. This month, I will share some tips on how to set up tail rotors. In an interview with Curtis Youngbood, the pioneer of 3D flying, he commented that the most important prerequisite to improving one’s flying is to have well-behaved yaw control.
A high-quality, carefully set-up tail rotor system improves the enjoyment and precision of flight.
How does one know whether the gyro is in the rate or heading-lock mode? This can be checked on the workbench by moving the tail rotor control stick to the left or right then releasing the stick. If the tail rotor blade pitch angle returns to where it was after the stick is released, the gyro is in the rate mode. If the blade pitch does not return to where it was, the gyro is in the heading-lock mode. The transmitter switch for channel 5 or the gear channel is usually used to toggle between the rate mode and heading-lock mode.
Both rate mode and heading-lock mode will let the gyro keep the helicopter heading steady. The difference is in the heading-lock mode. The gyro will keep the helicopter locked onto a heading that the pilot has commanded, but it will still allow the helicopter to yaw when the pilot moves the rudder stick. In the rate mode, the gyro will only dampen any drift in heading, but the heading might still drift.
It is called rate mode because the gyro lets your rudder control stick command a spin rate proportional to the amount of stick displacement. In heading-lock mode, the rudder stick initially commands a yaw angle then changes to commanding a spin rate (technically, it is called lagged-rate feedback). Nowadays, we prefer to fly in the heading-lock mode, which is necessary for backward flight.
Stefanie’s perfectly set-up KDS Agile 7.2 heli hovers as though a vise grip was holding it in the air.
To troubleshoot this, remove the main rotor and tail rotor blades, spool up the throttle in normal mode, and watch to see if the tail servo arm hunts. Turn on Idle-Up 1 and watch the tail servo arm again then turn on Idle-Up 2. While the motor is spinning, touch the side frame of the helicopter at various places to feel for vibration. I had one new electric motor that was slightly out of balance, and it was possible to feel the motor vibration induced on the carbon-fiber side frame. After balancing the outrunner motor casing, the vibration was reduced.
Some modern gyros, such as the Mikado VBar, have a frequency spectrum analyzer feature and permit the gyro to display the vibration intensity on a computer in real time. That feature is useful for balancing and reducing motor vibration.
The choice of a double-sided foam pad can have an effect on tail hunting. For example, my SAB Goblin 500 helicopter’s tail was perfectly smooth at normal throttle mode with the rotor at 2,000 rpm. In Idle-Up 1 at 2,200 rpm, the tail was still smooth. In Idle-Up 2 at 2,400 rpm, the tail rotor was madly hunting. When I tested the helicopter on the workbench without rotor blades, I could see the tail rotor servo arm hunt in Idle-Up 2. Replacing the 2 mm thick, soft foam tape with 1 mm foam tape stopped the hunting.
Another phenomenon that happens is that, in a hover, there is no tail hunting, but in a high-speed dive in idle-up mode, the tail hunts wildly. Reducing the gyro gain for idle-up mode by 5% to 10% eliminates the hunt. I use channel 5 in the transmitter to change gain values while flying.
Tail rotor blade stiffness and the airfoil shape can influence tail rotor control sensitivity and gyro effectiveness. Most plastic tail rotor blades have a sharp leading edge (LE), while carbon-fiber tail rotor blades have a blunt LE. A sharp LE makes tail rotor control more sensitive and twitchier near the center stick. There are usually no differences in the steady yaw rate between using a sharp LE versus a blunt LE tail blade. When using carbon-fiber tail blades, I normally do not use any exponential for tail rotor control. When using molded, plastic tail rotor blades, I might add 5% to 10% exponential.
Stefanie Sanchez is shown with her beautifully flying KDS Agile 7.2 helicopter.
Tail Rotor Mechanical and Transmitter Setup
To achieve a precise and smooth heading control, it is essential for the tail rotor control mechanism to move smoothly and without slop. Clean and lubricate the tail pitch-change mechanism and bellcrank bearings often. Periodically pop off the plastic ball link for the tail rotor control at the tail rotor bellcrank side then move the bellcrank by hand to see if the mechanism can glide smoothly. When you move the bellcrank a tiny amount by hand, the tail rotor blade pitch should also change slightly without free play. Connect the tail pushrod at the tail bellcrank and check the smoothness again by moving the tail control rod by hand at the servo end. If there is any binding, the source must be corrected. If your transmitter has a revolution mixing function, always leave that inhibited. I recommend starting with a 100% end-point value for left and right rudder stick. Check to see if the tail rotor servo arm is centered when the transmitter and receiver are switched on. It is easier to check the centering by putting the gyro in the rate mode. With most electronic flybarless controllers or heading-lock tail gyros, it is possible to choose between the rate or heading-lock mode for tail rotor control.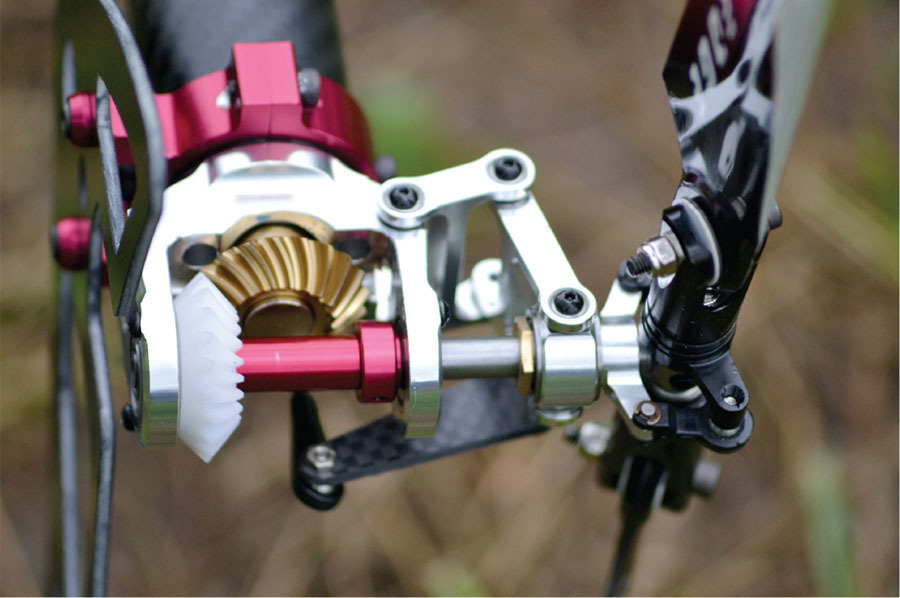
Flight Tuning
When the heli is in a steady hover, use the transmitter switch from heading-lock mode to rate mode. If it slowly yaws its nose to the left, it implies a need to mechanically increase the tail rotor blade pitch angle at hover. If it yaws to the right, reduce the pitch. Do this check when hovering in both normal and idle-up modes. The tail blade pitch angle should typically be at approximately 15° when the rudder stick is in the center. The purpose of this exercise is to give a mechanically symmetric setup. It is not possible to conduct this exercise in the heading-lock mode because the gyro will keep the helicopter heading fixed. Next, check to make sure that a full tail rotor command will make the helicopter spin at the same rate to the left and right. In a hover, do a full-speed pirouette to the left, and then to the right. You can perform this test with the heading-lock mode on. From the transmitter, increase the travel end-point value for the direction in which the pirouette is slower. After adjusting the end point, if the helicopter still spins slower in one direction, there is a mechanical issue of insufficient travel throw in one direction. This can also cause the helicopter to pirouette slower or stop less crisply when spinning in one of the directions. The mechanical travel can be changed in the flybarless gyro menu. Do not use the transmitter travel end point because that controls the "steady state" pirouette spin rate.Troubleshooting
During a hover, if the helicopter tail oscillates quickly, it means that the gyro gain is too high and the tail is "hunting." Turn down the gyro gain at 5% increments until the hunting stops. Sometimes the tail might not hunt when the helicopter is in a hover, but hunting starts when idle-up is turned on and the rotor rpm is high. This implies that there is a vibration issue and the flybarless gyro is being shaken.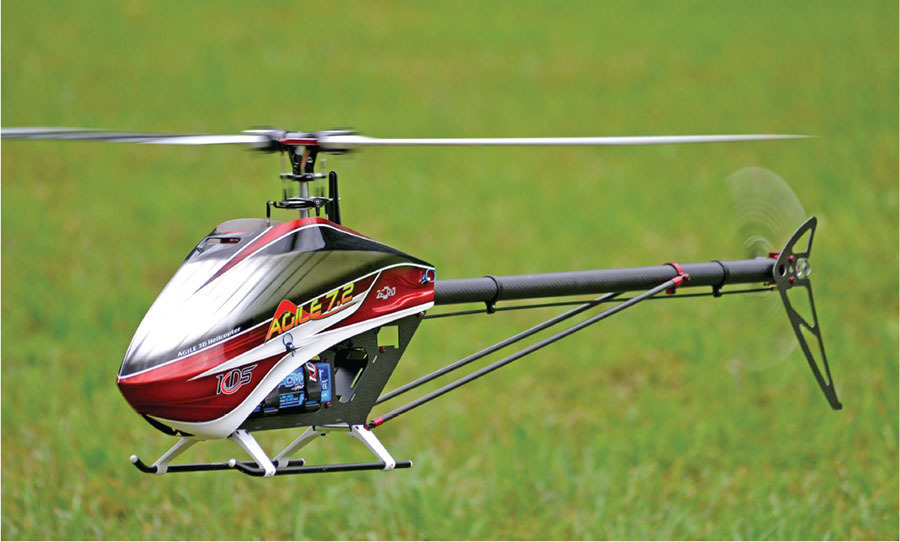
Listen to Your Helicopter
A slight bent-in tail rotor output shaft usually causes tailboom vibration. In the worst case, it could cause the entire helicopter to shake. Develop a habit of listening to your helicopter during flight. Any subtle difference in sound is a warning that something has changed. If the tail rotor shaft is slightly bent, the sound from the tail rotor will change. If something is loose on the helicopter, the stiffness of the airframe will change and modify the vibration characteristic, introducing a subtle vibrating noise. If you suddenly hear some noise on the helicopter, hit the throttle hold and land immediately. Throttle hold also helps reduce rotor rpm and stops the motor from putting energy into the system. See you next time.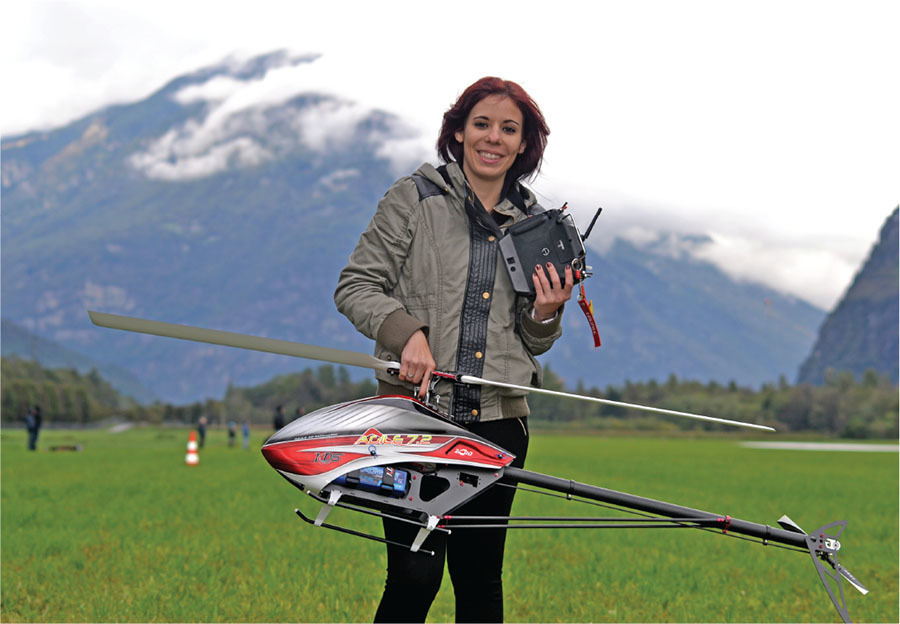
Comments
Tail Rotor
Does this information also apply to scale helicopters
Add new comment